Las fábricas de escáneres de huellas dactilares en China están experimentando un aumento en la demanda de sus productos debido a la creciente adopción de tecnología biométrica con fines de seguridad e identificación. Muchas de estas fábricas están ubicadas en los centros tecnológicos de Shenzhen y Guangzhou.
Los principales fabricantes de escáneres de huellas dactilares en China, como HFSECURITY, están produciendo una gama de productos de identificación biométrica, incluidos escáneres de huellas dactilares, sistemas de control de acceso y sistemas de control de asistencia.
Estas fábricas han invertido mucho en investigación y desarrollo para producir productos de alta calidad que cumplan con los estrictos requisitos de seguridad y precisión de sus clientes. También han implementado sólidas medidas de control de calidad para garantizar que cada escáner de huellas dactilares que producen cumpla con los estándares requeridos.

Además de satisfacer la demanda local, muchas de estas fábricas también exportan sus productos a otros países, incluidos Estados Unidos, Europa y Asia, lo que ha ayudado a posicionar a China como un fabricante líder de productos de identificación biométrica en el mercado global.
A pesar de los desafíos planteados por la pandemia de COVID-19, estas fábricas han seguido operando a plena capacidad, impulsadas por la creciente demanda de tecnología biométrica en diversas industrias, incluido el gobierno, las finanzas, la atención médica y el comercio minorista.
En general, la industria de fabricación de escáneres de huellas dactilares en China está prosperando, con una inversión continua en investigación y desarrollo, control de calidad y expansión global, lo que los posiciona como líderes en la industria de identificación biométrica.
Por supuesto, aquí hay 20 consejos para elegir una fábrica de escáneres de huellas dactilares en China:
1. Investigue a fondo las fábricas potenciales para asegurarse de que sean legítimas y confiables.
Al investigar posibles fábricas, es importante tomar las medidas necesarias para garantizar que sean legítimas y confiables. A continuación, se indican algunos pasos que puede seguir para realizar una investigación exhaustiva de las fábricas:
Realizar investigaciones en línea:
Comience por realizar una investigación en línea sobre la fábrica, incluido su sitio web, páginas de redes sociales y cualquier reseña o comentario de clientes anteriores. Esto le dará una idea de su reputación y experiencia.
Verificar certificaciones:
Busque certificaciones o acreditaciones que pueda tener la fábrica, como certificaciones ISO, para verificar sus estándares de calidad y cumplimiento.
Solicitar visitas a fábrica:
Solicite una visita a la fábrica en persona o programe una visita virtual. Esto le permitirá comprender mejor sus operaciones, capacidades de producción y la calidad de sus productos.
Verificar el registro empresarial:
Verifique el registro comercial de la fábrica con el gobierno local o las autoridades pertinentes para confirmar su estatus legal.
Solicitar referencias:
Pida referencias a clientes o proveedores anteriores que hayan trabajado con la fábrica. Póngase en contacto con estas referencias y pídales su opinión y experiencia con la fábrica.
Realizar verificaciones de antecedentes:
Realizar verificaciones de antecedentes de la fábrica, incluido su historial financiero y cualquier disputa legal en la que pueda haber estado involucrada.
Utilice una empresa de inspección de terceros:
Considere utilizar una empresa de inspección de terceros para realizar controles de calidad durante el proceso de producción para garantizar que los productos cumplan con sus estándares.
Siguiendo estos pasos, podrá realizar una investigación exhaustiva sobre posibles fábricas y asegurarse de estar trabajando con un socio legítimo y confiable.
2. Busque fábricas que se especialicen en escáneres de huellas dactilares y que tengan un historial comprobado de calidad.
Existen varias fábricas que se especializan en escáneres de huellas dactilares y tienen un historial comprobado de calidad. Estas son algunas opciones que se pueden considerar:
HFSECURITY-
HFSECURITY - HFSECURITY es líder mundial en tecnología de verificación biométrica, especializada en escáneres de huellas dactilares, sistemas de reconocimiento facial y soluciones de control de acceso. Se centran en la investigación y el desarrollo, y sus productos son conocidos por su alto rendimiento y fiabilidad.
Al seleccionar una fábrica para escáneres de huellas dactilaresEs importante tener en cuenta factores como la calidad del producto, el servicio de atención al cliente y las políticas de garantía. También es una buena idea leer las opiniones de los clientes e investigar la historia y la reputación de la empresa antes de tomar una decisión final.
3. Verificar si la fábrica cuenta con las certificaciones necesarias y el cumplimiento de los estándares de la industria.
Sí, es importante comprobar si la fábrica cuenta con las certificaciones necesarias y cumple con los estándares de la industria al momento de seleccionar un fabricante de escáneres de huellas dactilares. A continuación, se indican algunas certificaciones y estándares comunes que se deben buscar:
Certificación ISO: la certificación de la Organización Internacional de Normalización (ISO) garantiza que la fábrica ha cumplido con estándares específicos del sistema de gestión de calidad. La norma más relevante para los escáneres de huellas dactilares es la ISO 9001, que se centra en la gestión de calidad.
-724x1024.jpg)
Certificación del FBI: la certificación del FBI garantiza que el escáner de huellas dactilares cumple con estándares específicos de calidad de imagen e interoperabilidad con los sistemas del FBI. Esta certificación es particularmente importante para los escáneres de huellas dactilares utilizados en aplicaciones de aplicación de la ley.
Marcado CE: el marcado CE es una marca de certificación que indica el cumplimiento de las normas de la Unión Europea (UE) en materia de salud, seguridad y protección del medio ambiente. Es importante para los fabricantes que venden escáneres de huellas dactilares en el mercado de la UE.
Cumplimiento de la directiva RoHS: la directiva de restricción de sustancias peligrosas (RoHS) restringe el uso de determinadas sustancias peligrosas en equipos electrónicos y eléctricos. Este cumplimiento es especialmente importante para los escáneres de huellas dactilares que contienen componentes electrónicos.
Certificación UL: Underwriters Laboratories (UL) es una organización de certificación independiente que prueba y certifica productos en cuanto a seguridad y rendimiento. La certificación UL garantiza que el escáner de huellas dactilares cumple con estándares de seguridad específicos.
Es importante tener en cuenta que las certificaciones y estándares específicos requeridos
Puede variar según la aplicación y la industria. Por lo tanto, es una buena idea investigar las certificaciones y normas pertinentes para su caso de uso específico y asegurarse de que la fábrica que seleccione haya obtenido las certificaciones y el cumplimiento necesarios.
4. Elija una fábrica que tenga experiencia y haya estado en la industria durante un tiempo considerable.
Sin embargo, al elegir una fábrica, siempre es aconsejable tener en cuenta su nivel de experiencia y cuánto tiempo llevan operando en la industria.
Es probable que una fábrica con experiencia tenga una buena reputación en la industria y pueda ofrecer un mayor nivel de control de calidad y consistencia del producto. Han tenido tiempo para perfeccionar sus procesos y desarrollar experiencia en su área específica de producción, lo que puede dar como resultado mejores productos y tiempos de entrega más rápidos.
Además, una fábrica con un historial comprobado de proyectos exitosos y clientes satisfechos tiene más probabilidades de ser un socio confiable y digno de confianza para su negocio.
Al seleccionar una fábrica, siempre es esencial realizar una investigación exhaustiva, leer reseñas y solicitar referencias para asegurarse de que está trabajando con una empresa confiable y con experiencia que pueda satisfacer sus necesidades y expectativas.
5. Busque una fábrica que tenga la última tecnología y equipos para producir escáneres de huellas dactilares.
Sin embargo, puedo sugerirte algunos pasos que puedes seguir para encontrar dicha fábrica:
Busque en Internet: puede comenzar buscando en Internet empresas que se especialicen en la fabricación de escáneres de huellas dactilares. Utilice motores de búsqueda como Google, Bing o Yahoo para encontrar información relevante.
Asociaciones industriales:
Consulte las asociaciones industriales relacionadas con Tecnología biométrica o sistemas de seguridadEstas asociaciones a menudo proporcionan información sobre las empresas miembros y sus productos.
Ferias y exposiciones:
Asista a ferias y exposiciones relacionadas con la industria de la tecnología biométrica. Estos eventos suelen brindar la oportunidad de conocer a fabricantes y proveedores de escáneres de huellas dactilares.
Contactar con los fabricantes:
También puede contactar directamente con los fabricantes de escáneres de huellas dactilares y preguntar sobre su tecnología y equipos.
Publicaciones de la industria:
Busque publicaciones del sector que cubran la tecnología biométrica o los sistemas de seguridad. Estas publicaciones suelen incluir artículos sobre las últimas tecnologías y equipos del sector.
Recuerde comparar las características, la calidad y el costo de los diferentes escáneres de huellas dactilares antes de elegir un fabricante. Además, tenga en cuenta la reputación y el servicio de atención al cliente del fabricante antes de realizar una compra.
6. Pide referencias de clientes anteriores y revisa sus opiniones.
Sin embargo, si estás buscando referencias y reseñas de un producto o servicio, puedo sugerirte algunas formas de encontrarlas:
Consulte las reseñas en línea:
Busque el producto o servicio en sitios web de reseñas como Yelp, Google Reviews o Trustpilot. Estos sitios permiten a los clientes dejar reseñas y calificaciones, lo que puede darle una idea de la calidad del producto o servicio.

Solicitar referencias:
Si trabaja con una empresa o un particular, pídales referencias de clientes anteriores. Póngase en contacto con las referencias y pregúnteles sobre su experiencia con el producto o servicio.
Revisa las redes sociales:
Consulta las páginas de redes sociales de la empresa para ver reseñas o testimonios de clientes. Muchas empresas también tienen una sección de “reseñas” en su página de Facebook.
Pregúntele a sus amigos y familiares:
Pregunte a sus amigos y familiares si tienen alguna experiencia con el producto o servicio y si lo recomendarían.
Al realizar una pequeña investigación, puede obtener información valiosa sobre la calidad y confiabilidad de un producto o servicio antes de realizar una compra o comprometerse a trabajar con una empresa o individuo.
7. Asegúrese de que la fábrica tenga un sólido proceso de control de calidad para garantizar la consistencia de sus productos.
Asegurarse de que una fábrica cuente con un sólido proceso de control de calidad es un paso importante para garantizar la uniformidad de sus productos. A continuación, se indican algunos pasos que puede seguir para asegurarse de que la fábrica cuente con un sólido proceso de control de calidad:
Consulte las certificaciones de control de calidad de la fábrica:
Muchas fábricas cuentan con certificaciones de control de calidad, como la ISO 9001, que demuestran que han implementado un sistema de gestión de calidad. Estas certificaciones indican que la fábrica ha establecido y sigue un proceso de control de calidad estandarizado.
Busque evidencia de procedimientos de control de calidad:
Pídale a la fábrica que le proporcione documentación que describa sus procedimientos de control de calidad, incluyendo cómo prueban sus productos y qué medidas toman para garantizar la consistencia. Busque evidencia de que tienen procedimientos específicos implementados para prevenir la aparición de defectos o problemas de calidad.
Pregunte sobre su proceso de prueba:
Pregúntele a la fábrica sobre el proceso de prueba que utilizan para garantizar la consistencia de sus productos. Por ejemplo, ¿tienen un proceso de prueba estandarizado para cada producto y prueban cada producto antes de que salga de la fábrica?
Solicitar muestras:
Solicite muestras de los productos de la fábrica y examínelas detenidamente para asegurarse de que cumplan con sus estándares de calidad. Si es posible, solicite a un tercero independiente que analice las muestras para verificar su calidad.
Al seguir estos pasos, puede asegurarse de que la fábrica con la que trabaja tenga un sólido proceso de control de calidad para garantizar la consistencia de sus productos.
8. Verifique si la fábrica tiene la capacidad para satisfacer sus necesidades de producción.
Es importante asegurarse de que la fábrica con la que trabaja tenga la capacidad de satisfacer sus necesidades de producción. A continuación, se indican algunos pasos que puede seguir para determinar si la fábrica tiene la capacidad de satisfacer sus necesidades:
Evaluar la capacidad de producción actual de la fábrica:
Pregunte a la fábrica sobre su capacidad de producción actual y su posibilidad de ampliarla si es necesario. Determine si su capacidad actual puede satisfacer sus requisitos de producción o si tienen la posibilidad de aumentar su capacidad para satisfacer sus necesidades.
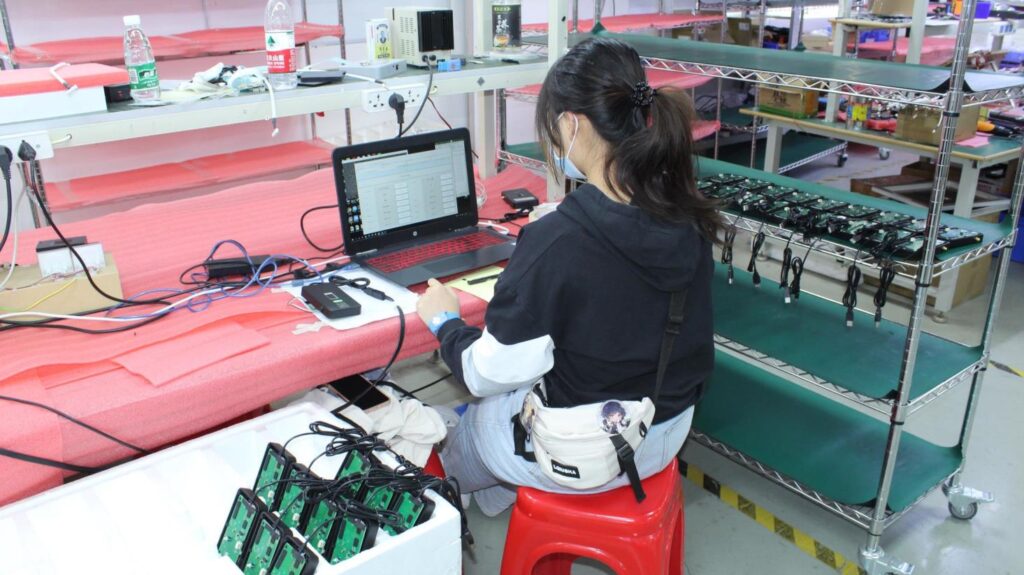
Determinar su plazo de entrega:
Pregúntele a la fábrica cuál es su plazo de producción. El plazo de producción es el tiempo que tarda la fábrica en producir y entregar el producto. Determine si su plazo de producción se ajusta a su cronograma de producción y si pueden entregar los productos a tiempo.
Evalúe sus equipos y tecnología:
Verifique el equipo y la tecnología de la fábrica para asegurarse de que cuentan con la maquinaria necesaria para producir su producto. Determine si cuentan con el equipo necesario para producir productos de alta calidad de manera eficiente.
Solicitar un plan de producción:
Solicite a la fábrica un plan de producción que describa su cronograma de producción, la cantidad de productos que pueden producir y los tiempos de entrega estimados. Esto le dará una mejor idea de la capacidad de la fábrica para satisfacer sus requisitos de producción.
Al seguir estos pasos, puede determinar si la fábrica tiene la capacidad para satisfacer sus requisitos de producción y asegurarse de que pueda producir la cantidad de productos que necesita de manera oportuna y eficiente.
9. Busque una fábrica que tenga un buen conocimiento de las especificaciones y requisitos de su producto.
Encontrar una fábrica que comprenda bien las especificaciones y los requisitos de sus productos es importante para garantizar que puedan producir productos de alta calidad que satisfagan sus necesidades. A continuación, se indican algunos pasos que puede seguir para encontrar una fábrica que comprenda bien las especificaciones y los requisitos de sus productos:
Proporcionar especificaciones detalladas del producto:
Proporcione a la fábrica especificaciones detalladas del producto que describan el diseño, los materiales, las dimensiones y cualquier otro detalle relevante. Esto ayudará a la fábrica a comprender mejor los requisitos de su producto.
Solicitar muestras:
Solicite muestras a la fábrica para asegurarse de que comprenden las especificaciones de su producto y pueden producir un producto que cumpla con sus estándares de calidad. Inspeccione las muestras con cuidado para asegurarse de que cumplan con sus especificaciones.
Comunicarse regularmente:
Es importante comunicarse regularmente con la fábrica para asegurarse de que comprendan bien las especificaciones y los requisitos de su producto. Mantenga una comunicación abierta con la fábrica para aclarar cualquier pregunta o inquietud que puedan tener.
Verifique la experiencia en su industria:
Busque una fábrica que tenga experiencia en la producción de productos en su sector. Ellos comprenderán mejor los requisitos de sus productos y estarán mejor equipados para producir productos de alta calidad que satisfagan sus necesidades.
Al seguir estos pasos, podrá encontrar una fábrica que comprenda bien las especificaciones y requisitos de su producto y asegurarse de que pueda producir productos de alta calidad que satisfagan sus necesidades.

10. Verifique si la fábrica cuenta con un equipo de I+D interno que pueda ayudarlo con la personalización y el desarrollo del producto.
Comprobar si la fábrica cuenta con un equipo interno de I+D puede ser una gran ventaja para la personalización y el desarrollo de productos. A continuación, se indican algunos pasos que puede seguir para determinar si la fábrica cuenta con un equipo interno de I+D:
Pregúntele a la fábrica:
Pregunte en la fábrica si cuentan con un equipo interno de I+D. Ellos podrán decirle si cuentan con un equipo dedicado a la investigación y el desarrollo.
Consulta su sitio web: consulta el sitio web de la fábrica para ver si tienen una sección dedicada a la investigación y el desarrollo. Esto puede indicar que cuentan con un equipo interno.
Consulte su oferta de productos:
Analice la oferta de productos de la fábrica para ver si ofrece productos personalizados o servicios de desarrollo de productos. Si es así, es probable que cuente con un equipo de I+D interno.
Solicita una reunión con su equipo de I+D:
Si la fábrica cuenta con un equipo de I+D interno, solicite una reunión con ellos para analizar sus necesidades de personalización o desarrollo de productos. Esto le permitirá hacerse una idea más clara de sus capacidades y experiencia.
Contar con un equipo de I+D interno puede ser beneficioso, ya que puede brindar asistencia técnica, asesoramiento sobre materiales y diseño, y ayudar con la personalización y el desarrollo de productos. Al tomar estas medidas, puede determinar si la fábrica cuenta con un equipo de I+D interno y asegurarse de que tenga las capacidades necesarias para satisfacer sus necesidades de personalización y desarrollo de productos.
11. Busque una fábrica que pueda ofrecer precios competitivos sin comprometer la calidad.
Para encontrar una fábrica que pueda ofrecer precios competitivos sin comprometer la calidad, es necesario investigar y hacer las debidas diligencias. A continuación, se indican algunos pasos que puede seguir para encontrar una fábrica de este tipo:
Realizar investigaciones en línea:
Utilice motores de búsqueda y directorios en línea para encontrar posibles fábricas que puedan ofrecer el producto o servicio que necesita. Busque fábricas que tengan críticas y calificaciones positivas, así como aquellas que tengan experiencia trabajando con empresas similares a la suya.
Contacte con varias fábricas:
Comuníquese con varias fábricas para solicitar cotizaciones e información sobre sus precios, capacidades de producción y medidas de control de calidad. Asegúrese de pedir referencias y muestras de su trabajo para ayudarlo a evaluar la calidad de sus productos.
Considere la ubicación de la fábrica:
Si es posible, trate de encontrar una fábrica que esté ubicada cerca de su negocio. Esto puede ayudar a reducir los costos de envío y los plazos de entrega, lo que puede ser especialmente importante si necesita realizar pedidos con frecuencia.
Busque una fábrica con buena reputación: investigue la reputación de las fábricas que está considerando. Verifique su presencia en línea, lea reseñas y hable con otras empresas que hayan trabajado con ellas anteriormente. Es más probable que una fábrica con buena reputación ofrezca productos de calidad a un precio competitivo.
Negociación de precios: Una vez que hayas recibido cotizaciones de varias fábricas, compáralas y negocia con las que ofrezcan la mejor combinación de calidad y precio. Ten en cuenta que la opción más barata puede no ser siempre la mejor a largo plazo, ya que los productos de mala calidad pueden generar costos adicionales y dañar tu reputación.
En general, encontrar una fábrica que ofrezca precios competitivos sin comprometer la calidad requiere cierta investigación y diligencia debida. Tómese el tiempo para comparar diferentes opciones y evaluar su reputación, medidas de control de calidad y capacidades de producción para tomar una decisión informada.
12. Verifique si la fábrica tiene un buen sistema de gestión de la cadena de suministro para garantizar una entrega oportuna.
Para comprobar si una fábrica cuenta con un buen sistema de gestión de la cadena de suministro, puede seguir estos pasos:
Pregunte sobre su proceso de gestión de la cadena de suministro: cuando esté en contacto con la fábrica, pregunte sobre su proceso de gestión de la cadena de suministro. Esto le dará una idea de cómo gestionan a sus proveedores, inventario y logística.
Verifique las relaciones con sus proveedores: el sistema de gestión de la cadena de suministro de una fábrica es tan bueno como sus relaciones con los proveedores. Pregúntele a la fábrica sobre sus relaciones con sus proveedores y cómo garantizan la entrega oportuna de los materiales.
Busque medidas de control de calidad: una fábrica con una buena gestión de la cadena de suministro tendrá medidas de control de calidad implementadas para garantizar que los materiales que recibe de los proveedores cumplan con sus estándares. Pregúntele a la fábrica sobre sus medidas de control de calidad y cómo garantizan que los materiales se entreguen a tiempo y en las condiciones adecuadas.
Pregunte sobre sus capacidades logísticas: una fábrica con un buen sistema de gestión de la cadena de suministro tendrá sólidas capacidades logísticas. Pregúntele a la fábrica sobre sus métodos de transporte y entrega y cómo garantizan que los productos se entreguen a tiempo.
Busque certificaciones: Certificaciones como ISO 9001:2015 e ISO 14001:2015 pueden ser una indicación de que una fábrica tiene implementado un buen sistema de gestión de la cadena de suministro. Busque estas certificaciones en el sitio web de la fábrica o pregúntele si las tienen.
En general, una fábrica con un buen sistema de gestión de la cadena de suministro podrá garantizar la entrega oportuna de los productos. Si pregunta sobre el proceso de gestión de la cadena de suministro de la fábrica, las relaciones con los proveedores, las medidas de control de calidad, las capacidades logísticas y las certificaciones, podrá hacerse una mejor idea de si la fábrica puede cumplir con sus requisitos de entrega.
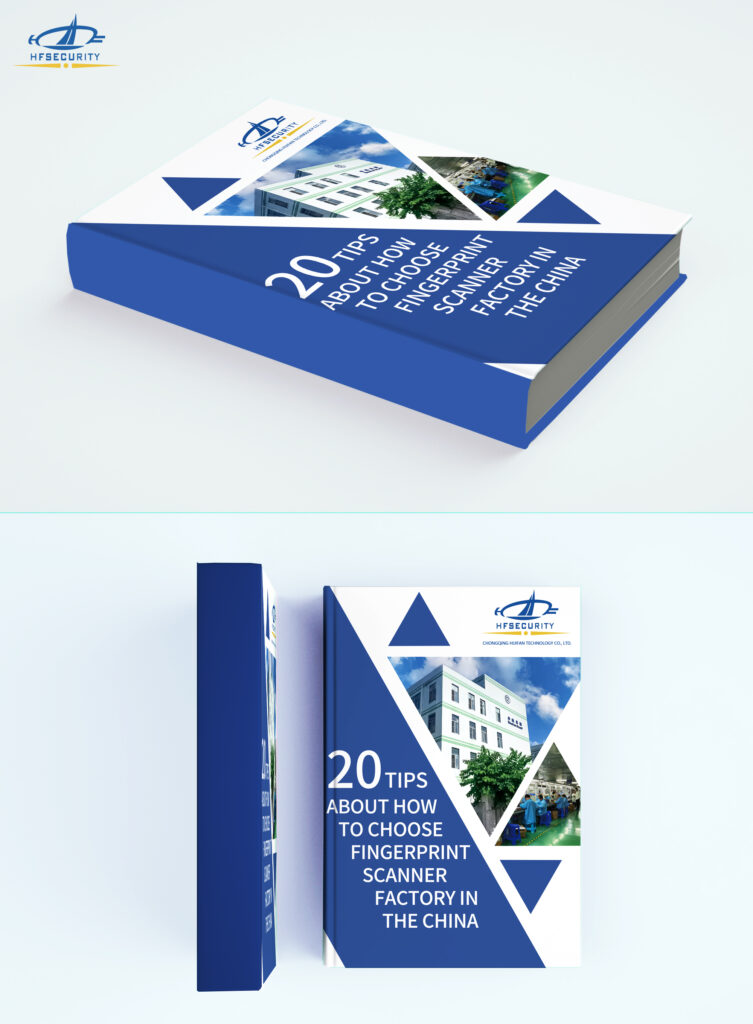
13. Pregunte sobre las políticas de garantía y soporte posventa de la fábrica.
Para preguntar sobre las políticas de garantía y soporte posventa de la fábrica, aquí hay algunas preguntas que puedes hacer:
¿Cuál es su política de garantía?
Pregúntele a la fábrica sobre su política de garantía. ¿Cuánto dura el período de garantía? ¿Qué tipos de problemas cubre la garantía? ¿Cómo maneja la fábrica los reclamos de garantía?
¿Cuál es su política de soporte posventa?
Pregúntele a la fábrica sobre su política de soporte posventa. ¿Tienen un equipo de soporte dedicado? ¿Qué tipos de servicios posventa ofrecen? ¿Cómo manejan las quejas o problemas de los clientes?
¿Cuál es su política de devolución?
Pregúntele a la fábrica sobre su política de devoluciones. ¿Se aceptan devoluciones? Si es así, ¿bajo qué condiciones? ¿Quién cubre el costo de las devoluciones?
¿Cómo se gestionan las reparaciones o sustituciones?
Pregúntele a la fábrica cuál es su política para manejar reparaciones o reemplazos. ¿Cuánto tiempo lleva obtener una reparación o reemplazo? ¿Quién cubre el costo de las reparaciones o reemplazos?
¿Puede proporcionarnos referencias o ejemplos de su soporte posventa?
Pregunte a la fábrica si pueden proporcionarle referencias o ejemplos de su servicio posventa. Esto puede darle una mejor idea de cómo manejan la atención y el servicio al cliente.
En general, es importante preguntar sobre las políticas de garantía y soporte posventa de la fábrica para asegurarse de recibir el soporte y la asistencia necesarios si surgen problemas con su producto. Al hacer estas preguntas, puede tomar una decisión informada sobre si las políticas de la fábrica satisfacen sus necesidades y requisitos.
14. Busque una fábrica que pueda proporcionarle muestras para realizar pruebas y evaluación.
A continuación se indican algunos pasos generales que puede seguir para encontrar una fábrica que pueda proporcionar muestras para pruebas y evaluación:
Identifique el tipo de producto que desea fabricar y determine las especificaciones y requisitos.
Busque en línea fabricantes o fábricas que se especialicen en producir el tipo de producto que necesita.
Comuníquese con las fábricas que haya seleccionado y pregúnteles si pueden proporcionarle muestras para probarlas y evaluarlas.
Proporcionar a la fábrica las especificaciones y requisitos del producto, junto con cualquier información adicional que puedan necesitar, como la cantidad de muestras requeridas, su presupuesto y la fecha límite de entrega.
Una vez que reciba las muestras, pruébelas y evalúelas para asegurarse de que cumplen con sus requisitos.
También puede considerar asistir a ferias comerciales y exposiciones relacionadas con su industria para conectarse con posibles proveedores y fabricantes.
15. Verifique si la fábrica puede ofrecer opciones de personalización, como marca y embalaje.
Para comprobar si una fábrica puede ofrecer opciones de personalización, como marca y embalaje, puede seguir estos pasos:
Comuníquese con la fábrica y pregunte si ofrecen opciones de personalización para la marca y el empaque.
Proporciónales tus requisitos específicos, como el tipo de marca o empaque que necesitas, el logotipo o diseño que deseas utilizar y cualquier otro requisito específico.
Solicite muestras o ejemplos de sus trabajos de personalización anteriores, si están disponibles, para evaluar sus capacidades y calidad.
Confirme los costos asociados con la personalización, incluidos los cargos adicionales o las cantidades mínimas de pedido que puedan aplicarse.
Negociar los términos de la personalización, incluidos los plazos, el pago y cualquier otro detalle que deba acordarse.
Si sigue estos pasos, debería poder determinar si la fábrica puede proporcionar las opciones de personalización que necesita para su producto.
16. Pregunte si la fábrica puede proporcionarle las certificaciones de producto requeridas para su mercado objetivo.
Para preguntar a una fábrica si puede proporcionarle las certificaciones de producto requeridas para su mercado objetivo, puede seguir estos pasos:
Identifique las certificaciones que necesita su producto para ingresar al mercado de destino. Estas pueden incluir certificaciones de seguridad, calidad, ambientales u otras certificaciones regulatorias.
Comuníquese con la fábrica y pregunte si tienen experiencia en la obtención de las certificaciones que necesita para su mercado objetivo.
Proporciónales las certificaciones específicas que necesitas y pregúntales si pueden ayudarte en el proceso de certificación.
Solicite ejemplos de otros proyectos que hayan completado y que requieran las mismas certificaciones, si están disponibles, para evaluar su experiencia y capacidades.
Confirme los costos asociados con la obtención de las certificaciones, incluidos los cargos o tarifas adicionales que puedan aplicarse.
Negociar los términos del proceso de certificación, incluidos los plazos, el pago y cualquier otro detalle que deba acordarse.
Si sigue estos pasos, podrá determinar si la fábrica puede proporcionarle las certificaciones de producto necesarias para su mercado objetivo.
17. Busque una fábrica que tenga buena comunicación y servicio al cliente.
Para encontrar una fábrica que tenga buena comunicación y servicio al cliente, puedes seguir estos pasos:
Investiga la fábrica en Internet y busca opiniones y valoraciones de clientes. Esto te puede dar una idea de su nivel de servicio al cliente y comunicación con los clientes.
Comuníquese con la fábrica y observe su tiempo de respuesta, su nivel de profesionalismo y su disposición a responder sus preguntas. Una fábrica que responde con prontitud y cortesía a sus consultas tiene más probabilidades de brindar un buen servicio al cliente y una buena comunicación.
Pida referencias a clientes anteriores y póngase en contacto con ellos para preguntarles sobre su experiencia trabajando con la fábrica. Esto puede brindarle información de primera mano sobre el nivel de servicio al cliente y comunicación de la fábrica.
Infórmese sobre sus canales de comunicación, como correo electrónico, teléfono o chat, y pregunte sobre su disponibilidad para responder preguntas o brindar actualizaciones sobre su proyecto.
Tenga en cuenta la barrera del idioma, especialmente si trabaja con una fábrica en otro país o región. Una fábrica que tenga personal que domine su idioma puede facilitar y hacer más eficaz la comunicación.
Evalúe su capacidad para cumplir con los plazos y las promesas. Una fábrica que sea transparente en cuanto a su proceso de producción y que pueda proporcionar actualizaciones periódicas sobre el estado de su proyecto puede ayudar a generar confianza en su servicio al cliente.
Si sigue estos pasos, debería poder encontrar una fábrica que ofrezca buena comunicación y servicio al cliente.
18. Verifique si la fábrica tiene una buena política de responsabilidad ambiental y social.
Para comprobar si una fábrica tiene una buena política de responsabilidad ambiental y social, puedes seguir estos pasos:
Investiga el sitio web de la fábrica y busca información sobre sus políticas de responsabilidad social y medioambiental. Esto puede incluir declaraciones sobre su compromiso con la sostenibilidad, la reducción de residuos, las prácticas laborales justas y otras iniciativas de responsabilidad social.
Busque certificaciones o auditorías de terceros que verifiquen el cumplimiento de la fábrica con las normas de responsabilidad social y medioambiental. Algunos ejemplos de certificaciones incluyen la ISO 14001 para la gestión medioambiental y la SA8000 para la responsabilidad social.
Pregúntele directamente a la fábrica sobre sus políticas y prácticas de responsabilidad social y medioambiental. Esto puede incluir preguntas sobre sus esfuerzos de reducción de residuos y reciclaje, sus prácticas laborales y su compromiso con el uso de materiales y procesos sostenibles.
Solicite información sobre su cadena de suministro y sobre los socios o proveedores con los que trabaja. Una fábrica comprometida con la responsabilidad ambiental y social también debería esperar lo mismo de sus socios y proveedores.
Si es posible, considere visitar la fábrica en persona para observar sus operaciones y evaluar de primera mano sus prácticas de responsabilidad ambiental y social.
Si sigue estos pasos, podrá determinar si una fábrica tiene una buena política de responsabilidad social y medioambiental. Elegir una fábrica que priorice la sostenibilidad y la responsabilidad social no solo puede beneficiar al medioambiente y a los trabajadores, sino que también puede ayudar a mejorar la reputación de su marca y atraer a clientes que compartan valores similares.
19. Busque una fábrica que pueda proporcionarle una variedad de tipos de escáneres de huellas dactilares que se adapten a sus necesidades.
Para buscar una fábrica que pueda proporcionarle una variedad de tipos de escáneres de huellas dactilares que se adapten a sus necesidades, puede seguir estos pasos:
Determine el tipo de escáner de huellas dactilares que necesita en función de su aplicación y sus requisitos. Puede incluir escáneres de huellas dactilares ópticos, capacitivos o ultrasónicos, así como módulos independientes o integrados.
Busque en Internet fabricantes o fábricas que se especialicen en producir el tipo de escáner de huellas dactilares que necesita. Busque aquellos que ofrezcan una variedad de tipos y modelos de escáneres para elegir.
Comuníquese con las fábricas que haya seleccionado y solicite información sobre sus productos de escáneres de huellas dactilares. Indíqueles sus requisitos específicos, incluida la cantidad de escáneres que necesita, su presupuesto y cualquier otro detalle que pueda ser relevante.
Solicite muestras o demostraciones de los escáneres de huellas dactilares para evaluar su rendimiento y calidad.
Confirme las opciones de personalización disponibles, como la marca o el empaque, si corresponde.
Infórmese sobre el soporte técnico de la fábrica y el servicio posventa, como opciones de garantía, reparación o reemplazo, para asegurarse de que puede confiar en su apoyo en caso de cualquier problema.
Si sigue estos pasos, debería poder encontrar una fábrica que pueda proporcionarle una variedad de tipos de escáneres de huellas dactilares que se adapten a sus necesidades.
20. Verifique si la fábrica tiene la documentación de exportación y la experiencia necesarias para enviar productos a nivel internacional.
Para comprobar si una fábrica tiene la documentación de exportación y la experiencia necesarias para enviar productos a nivel internacional, puede seguir estos pasos:
Infórmese sobre la experiencia de la fábrica en la exportación de productos a nivel internacional. Solicite ejemplos de envíos internacionales anteriores y a qué países han realizado envíos.
Confirme que la fábrica cuenta con las licencias y permisos de exportación necesarios para enviar productos a su país o región. Esto puede incluir declaraciones de aduanas, licencias de exportación y otra documentación.
Pregunte si la fábrica tiene experiencia trabajando con transportistas o transportistas internacionales para garantizar que sus productos se enviarán de manera segura y eficiente.
Confirme que la fábrica esté familiarizada con todas las regulaciones o restricciones relacionadas con la exportación de sus productos a su mercado objetivo, incluidos los requisitos de etiquetado, documentación o embalaje del producto.
Infórmese sobre los canales de comunicación de la fábrica para envíos internacionales, incluida información de seguimiento y actualizaciones sobre el estado de su envío.
Tenga en cuenta las tarifas o cargos adicionales que puedan aplicarse a los envíos internacionales, como aranceles aduaneros o impuestos, y confirme con la fábrica si pueden ayudar a calcular y pagar estas tarifas.
Si sigue estos pasos, podrá determinar si una fábrica cuenta con la documentación de exportación y la experiencia necesarias para enviar productos a nivel internacional. Trabajar con una fábrica que tenga experiencia en la exportación a su mercado objetivo puede ayudarle a garantizar que sus productos se envíen de manera segura, a tiempo y de conformidad con los requisitos reglamentarios.
Cómo elegir una fábrica de escáneres de huellas dactilares en China
Elegir una fábrica de escáneres de huellas dactilares en China puede ser una tarea difícil, pero aquí hay algunos consejos que le ayudarán a tomar una decisión informada:
Investigación:
Comience por investigar diferentes fábricas de escáneres de huellas dactilares en China. Puede utilizar directorios en línea, motores de búsqueda y asociaciones industriales para encontrar posibles proveedores. Busque fábricas con buena reputación, experiencia en la industria y antecedentes en la producción de productos de calidad.
Comprobar credenciales:
Una vez que tenga una lista de posibles fábricas, verifique sus credenciales. Compruebe si la fábrica está registrada ante las autoridades pertinentes, como la Cámara de Comercio de China para la Importación y Exportación de Maquinaria y Productos Electrónicos (CCCME), y si cuenta con las certificaciones necesarias, como ISO 9001 o CE.
Control de calidad:
Busque fábricas con un sistema de control de calidad sólido. Deben tener medidas establecidas para garantizar que cada escáner de huellas dactilares que producen cumpla con sus especificaciones y los estándares de la industria.
Capacidad de producción:
Compruebe si la fábrica tiene la capacidad para satisfacer sus necesidades de producción. ¿Pueden producir la cantidad necesaria de escáneres de huellas dactilares en el plazo deseado? ¿Disponen del equipo y la mano de obra necesarios para gestionar su pedido?
Comunicación:
Asegúrese de que la fábrica cuente con personal que pueda comunicarse en inglés o en su idioma preferido. La comunicación es fundamental para garantizar que su pedido se produzca según sus especificaciones y que cualquier problema se pueda resolver rápidamente.
Precios:
Si bien el precio es importante, no debería ser el único factor en tu decisión. Más barato no siempre significa mejor calidad, y deberías buscar un precio justo por la calidad del producto.
Visita la fábrica:
Si es posible, visite la fábrica para evaluar en persona sus procesos de producción, equipos y medidas de control de calidad. Esto le permitirá comprender mejor las capacidades de la fábrica y le ayudará a tomar una decisión informada.
Si sigue estos consejos, podrá encontrar una fábrica de escáneres de huellas dactilares confiable en China que pueda producir productos de calidad para satisfacer sus necesidades.
Resumen de fábrica de escáneres de huellas dactilares
Una fábrica de escáneres de huellas dactilares es una instalación de fabricación que produce dispositivos de autenticación biométrica que capturan y analizan patrones únicos de las huellas dactilares de una persona con fines de seguridad.
El proceso de producción de un escáner de huellas dactilares generalmente implica varios pasos, incluido el diseño y la ingeniería del escáner, la adquisición de materiales y componentes, el ensamblaje del dispositivo y la prueba y el control de calidad del producto terminado.
El escáner funciona utilizando un sensor para capturar la imagen de la huella dactilar de una persona, que luego se convierte en una plantilla digital que puede almacenarse y compararse con otras plantillas para fines de autenticación.
Los escáneres de huellas dactilares se utilizan comúnmente en una variedad de entornos, como para el control de acceso a áreas seguras, el seguimiento de tiempo y asistencia, y la seguridad de dispositivos móviles.
Se espera que el mercado de escáneres de huellas dactilares crezca en los próximos años debido a las crecientes preocupaciones sobre la seguridad y el robo de identidad, así como a la creciente adopción de tecnologías de autenticación biométrica en diversas industrias.
